Battery recycling represents a crucial cornerstone in our transition to a sustainable energy future, transforming potential environmental hazards into valuable resources through a sophisticated yet efficient process. The journey of sustainable battery recycling begins with collection and ends with the recovery of precious metals and materials, creating a circular economy that benefits both industry and environment.
In Australia, where battery usage continues to surge with the adoption of electric vehicles and renewable energy storage systems, understanding the battery recycling flowchart has never been more critical. From neighborhood collection points to advanced processing facilities, each step in the recycling chain plays a vital role in maximizing resource recovery while minimizing environmental impact.
This comprehensive guide breaks down the complex battery recycling process into clear, manageable stages, demonstrating how different battery types undergo specific treatment processes to extract valuable materials like lithium, cobalt, and nickel. Whether you’re an industry professional seeking to optimize your recycling operations or an environmentally conscious individual wanting to understand the journey of your recycled batteries, this flowchart provides the essential roadmap for responsible battery disposal and resource recovery.
The Journey Begins: Collection and Sorting
Collection Points and Methods
In Australia, battery collection points are strategically placed across urban and rural areas to make recycling convenient and accessible. Major retailers like Aldi, Officeworks, and Battery World serve as primary collection hubs, accepting used batteries during regular business hours. Local councils also maintain dedicated collection points at waste management facilities and community centres.
Mobile battery collection services operate in regional areas, ensuring remote communities can participate in recycling initiatives. Many workplaces and schools have implemented their own collection programs, contributing to the national recycling effort. These collection points typically use specially designed containers that safely store different battery types, from standard alkaline batteries to lithium-ion variants.
The Australian Battery Recycling Initiative (ABRI) has established a comprehensive network that connects these collection points with certified recycling facilities. When containers reach capacity, licensed transporters collect and deliver them to sorting facilities, ensuring safe handling throughout the journey. This efficient collection system has helped Australia achieve increasingly higher battery recycling rates, with some states reporting up to 90% collection rates for certain battery types.
To locate your nearest collection point, most local councils provide online search tools or mobile apps that map available drop-off locations in your area.
Battery Classification Process
The first crucial step in battery recycling involves accurate classification of different battery types. At Australian recycling facilities, trained operators use both manual inspection and automated sorting systems to categorize batteries based on their chemical composition and size. The main categories include lead-acid automotive batteries, lithium-ion batteries from electronics, nickel-cadmium batteries, and alkaline batteries.
Modern sorting facilities employ sophisticated technology such as X-ray fluorescence (XRF) scanners to identify battery chemistry quickly and accurately. These machines can process hundreds of batteries per minute, separating them into designated collection bins. Visual identification markers, such as size, shape, and labeling, also help in the initial sorting process.
A vital part of classification involves checking for damaged or leaking batteries, which require special handling procedures. These are isolated and processed separately to prevent contamination and ensure worker safety. The sorting process also identifies any batteries that might be suitable for refurbishment rather than recycling, supporting Australia’s commitment to the waste hierarchy principle of ‘reduce, reuse, recycle’.
Quality control checks throughout the classification process ensure accurate sorting, as different battery types require different recycling methods in subsequent stages.
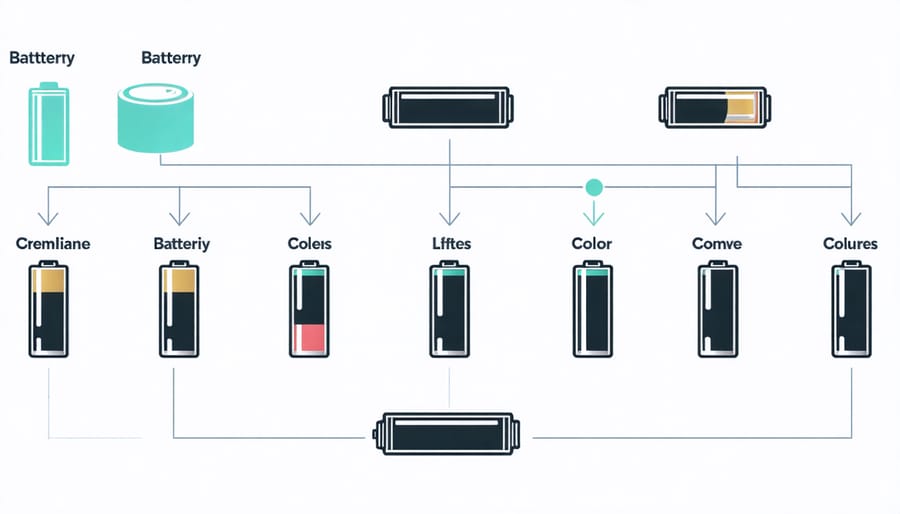
Breaking It Down: The Dismantling Process
Safety Protocols and Equipment
Battery recycling requires strict adherence to safety protocols to protect workers and the environment. All personnel must wear appropriate Personal Protective Equipment (PPE), including chemical-resistant gloves, safety goggles, face shields, and flame-resistant clothing. Protective footwear with anti-slip soles is essential when handling heavy battery components.
The dismantling area must be well-ventilated with proper air filtration systems to manage potentially harmful fumes. Emergency eyewash stations and chemical showers should be readily accessible, and spill containment kits must be strategically placed throughout the facility.
Fire safety is paramount, with specialized fire extinguishers designed for battery fires positioned at key locations. Temperature monitoring systems help prevent thermal runaway incidents, while proper storage containers with acid-resistant linings ensure safe handling of corroded batteries.
Australian standards require regular safety training for all workers, including proper handling techniques and emergency response procedures. Facilities must maintain clear evacuation routes and conduct regular emergency drills. Advanced sorting equipment helps minimize direct contact with hazardous materials, while automated systems assist in safely breaking down batteries.
Modern recycling facilities often incorporate smart sensors that detect dangerous gas levels and automatically trigger ventilation systems. All equipment must be regularly inspected and maintained to prevent mechanical failures that could compromise safety. Proper labelling and segregation of different battery types help prevent dangerous chemical reactions during processing.
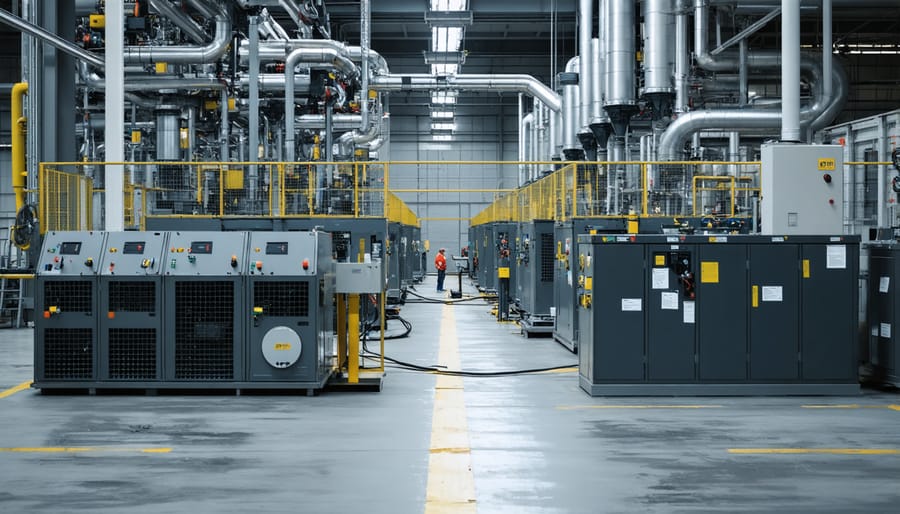
Component Separation
In the component separation phase, batteries undergo a careful dismantling process where various battery materials are isolated for efficient recycling. The process typically begins with mechanical separation, where batteries are fed into specialized crushing machines that break them down into smaller pieces while maintaining safety protocols to prevent chemical reactions.
Advanced sorting technologies, including magnetic separators, identify and extract ferrous metals like steel casings and magnetic components. Non-ferrous materials, such as copper and aluminium, are then separated using eddy current separation techniques. This clever bit of engineering uses magnetic fields to sort different metals based on their conductivity – a real ripper of an innovation that’s made recycling more efficient than ever.
The plastic components, including casings and separators, are isolated through density separation methods, often using water-based solutions. These materials float to the surface while heavier components sink, making for a clean separation. For lithium-ion batteries specifically, the valuable black mass containing critical minerals like lithium, cobalt, and nickel is carefully extracted and stored for further processing.
Modern Australian recycling facilities employ sophisticated optical sorting systems and artificial intelligence to ensure maximum recovery rates. This technology can identify different types of materials with incredible accuracy, ensuring that nothing goes to waste and every component finds its way to the right recycling stream.
Material Recovery and Processing
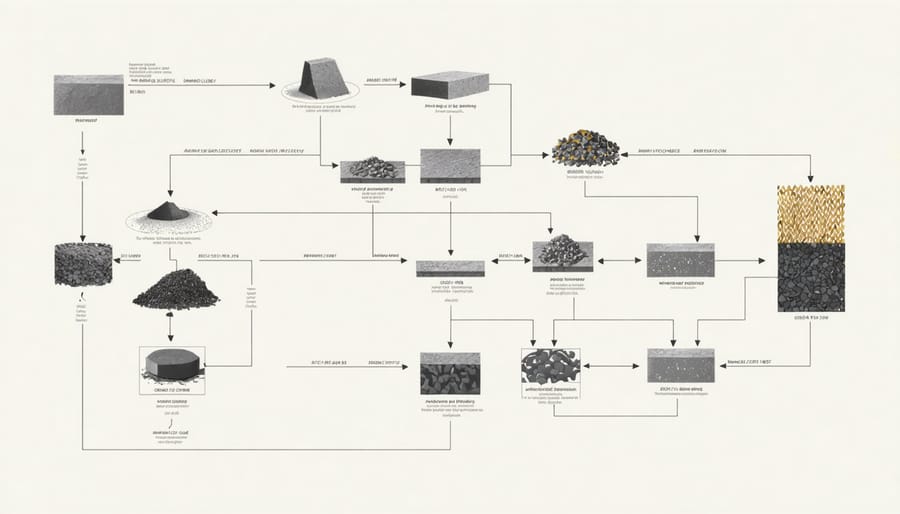
Metal Extraction Methods
In the metal extraction phase, several cutting-edge technologies work together to recover valuable metals from battery components. The most common method is hydrometallurgy, where batteries are immersed in specialised chemical solutions to dissolve and separate different metals. This process is particularly effective for recovering lithium, cobalt, and nickel, achieving recovery rates of up to 95%.
Another widely used technique is pyrometallurgy, which involves heating battery materials to extremely high temperatures. This method is brilliant for recovering copper and aluminium, though it’s typically used in conjunction with hydrometallurgy for optimal results. Australian recycling facilities have made significant strides in combining these methods to maximise metal recovery while minimising environmental impact.
Emerging technologies include bio-metallurgy, where specially cultivated bacteria help extract metals through natural processes. This innovative approach is gaining traction in Australia’s battery recycling industry due to its lower environmental footprint and reduced energy requirements.
The mechanical-chemical method is also making waves, using precise crushing and screening techniques followed by chemical separation. This approach is particularly effective for recovering rare earth elements and has shown promising results in pilot programs across Victoria and New South Wales.
Once extracted, these metals undergo purification processes to meet industry standards for reuse. The refined metals can then be used to manufacture new batteries or other products, creating a circular economy that reduces the need for raw material mining. Australian recyclers are achieving particularly impressive results with lithium and cobalt recovery, helping to position the country as a leader in sustainable battery recycling technology.
Material Purification
The material purification stage represents a crucial phase in battery recycling, where recovered materials are refined to meet industry standards for reuse. Through advanced hydrometallurgical processes, metals like lithium, cobalt, and nickel undergo thorough cleaning and separation to remove impurities. This involves a series of chemical treatments, including leaching, precipitation, and crystallisation, ensuring the materials meet strict quality benchmarks.
In Australian recycling facilities, the purification process typically begins with chemical dissolution, where recovered materials are treated with specific solvents to separate valuable components. These solutions then undergo filtration and extraction processes to isolate individual metals. For instance, copper and aluminium are purified through electrolysis, while lithium undergoes a carbonate precipitation process to achieve battery-grade quality.
Modern purification techniques employ sophisticated methods like solvent extraction and ion exchange to achieve high purity levels. These processes are particularly important for critical materials like cobalt and nickel, which must meet stringent specifications for battery manufacturing. Advanced Australian facilities are now achieving purification rates of up to 99.9% for key metals, making them suitable for direct reuse in new battery production.
Quality control plays a vital role throughout the purification process, with continuous monitoring and testing ensuring that recovered materials meet or exceed industry standards. This attention to detail has enabled Australian recyclers to produce materials that are indistinguishable from virgin resources, contributing to a more sustainable battery manufacturing cycle.
The success of material purification has been instrumental in closing the loop on battery recycling, demonstrating that recovered materials can effectively replace raw materials in new battery production, reducing our reliance on mining and mineral extraction.
Closing the Loop: From Waste to New Batteries
The journey of recycled battery materials doesn’t end at recovery – it’s just the beginning of a new lifecycle. The recovered materials, including valuable metals like lithium, cobalt, and nickel, become the building blocks for new batteries through a carefully orchestrated process of material refinement and integration into Australian battery manufacturing.
Once materials reach the required purity levels, they’re processed into active cathode and anode materials. These components are virtually indistinguishable from their virgin counterparts, offering the same high performance while significantly reducing environmental impact. In fact, recycled materials can make up to 90% of new battery contents, creating a genuine circular economy.
Leading Australian manufacturers are increasingly incorporating these recycled materials into their production lines, demonstrating that sustainability and performance can go hand in hand. The process not only reduces our reliance on mining but also creates local jobs and strengthens our domestic supply chain.
The integration of recycled materials involves rigorous quality control measures to ensure the new batteries meet or exceed industry standards. Advanced testing procedures verify the composition and performance of recycled materials before they’re approved for use in new products.
This closed-loop system represents a win-win situation: it reduces waste, conserves natural resources, and supports local industry growth. As battery technology continues to evolve, the efficiency of this recycling-to-manufacturing pipeline improves, making each new generation of batteries more sustainable than the last.
Battery recycling stands as a cornerstone of Australia’s clean energy revolution, offering a sustainable pathway to manage our growing energy storage needs. By implementing efficient recycling processes, we’re not just reducing waste – we’re creating a circular economy that benefits both the environment and our communities. The systematic approach to battery recycling helps recover valuable materials like lithium, cobalt, and nickel, which can be reused in manufacturing new batteries and other products.
This closed-loop system significantly reduces our dependence on raw material mining, cuts down greenhouse gas emissions, and creates local jobs in the recycling industry. As battery usage continues to grow across renewable energy systems, electric vehicles, and consumer electronics, the importance of these recycling processes becomes even more crucial.
The future of battery recycling in Australia looks promising, with innovative technologies and improved collection systems making the process more efficient and accessible. By participating in battery recycling programs, we’re all contributing to a more sustainable future while supporting our nation’s transition to renewable energy. Together, we can turn what was once considered waste into valuable resources for generations to come.