Energy Use Intensity (EUI) stands as the cornerstone metric revolutionizing how Australian industries measure and optimize their energy performance. This crucial indicator, measuring energy consumption per square meter of floor space annually, empowers organizations to make data-driven decisions that transform their energy landscape. By understanding and implementing EUI analysis, companies unlock the benefits of bioenergy integration while strategically reducing their carbon footprint.
As Australia accelerates toward its renewable energy targets, EUI serves as both a diagnostic tool and performance benchmark, helping facilities identify energy waste, prioritize efficiency upgrades, and validate sustainability investments. Forward-thinking organizations leveraging EUI analytics consistently achieve 20-30% energy savings while maintaining or improving operational output. This practical approach to energy management resonates particularly well with Australian industry leaders who recognize that measuring energy intensity is the first step toward meaningful sustainability transformation.
For facility managers and sustainability professionals, EUI provides the quantitative foundation needed to justify energy-efficient technologies, optimize building systems, and demonstrate tangible progress toward corporate environmental goals. Whether managing a single facility or overseeing a nationwide portfolio, EUI delivers the insights needed to drive strategic energy decisions that benefit both the bottom line and our planet’s future.
Understanding Energy Use Intensity in Industrial Settings
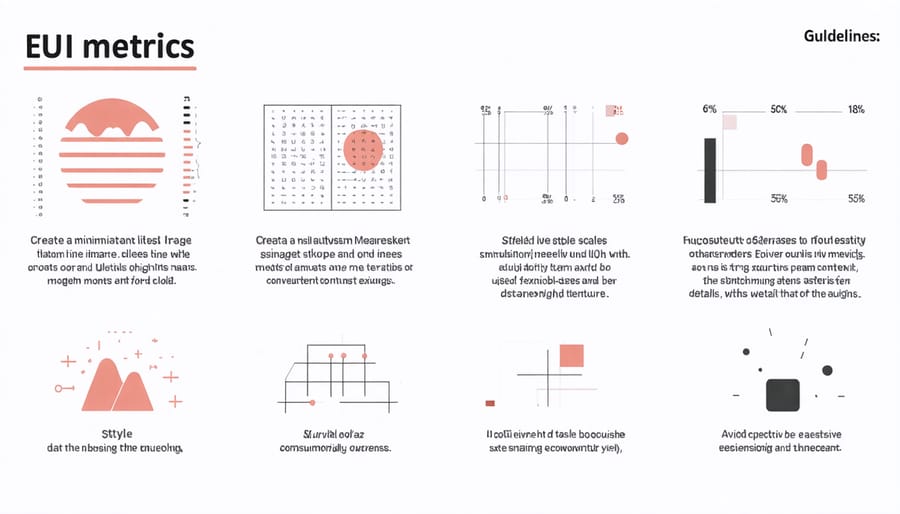
Key EUI Metrics for Bioenergy Systems
When evaluating bioenergy systems, several key energy efficiency measurements help determine their performance and environmental impact. The primary metric is the biomass-to-energy conversion rate, typically measured in gigajoules per tonne of feedstock. This indicates how effectively the system transforms organic material into usable energy.
Another crucial indicator is the net energy ratio (NER), which compares the energy output to the total energy input required for production, including harvesting, transportation, and processing. A well-designed bioenergy system should achieve an NER greater than 3:1 to be considered highly efficient.
Carbon intensity metrics, measured in CO2-equivalent per unit of energy produced, help assess the environmental benefits of bioenergy systems. Australian facilities often aim for less than 20g CO2e/MJ to maintain competitive advantage in the renewable energy sector.
System availability and reliability indices track operational efficiency, with leading facilities maintaining uptime rates above 85%. The feedstock consumption rate and moisture content are also vital metrics, as they directly impact system performance and operating costs. Modern Australian bioenergy plants typically optimize for feedstock moisture levels between 20-30% to achieve maximum efficiency.
These indicators work together to provide a comprehensive picture of bioenergy system performance, helping operators make informed decisions about system improvements and maintenance schedules.
Australian Industry Standards and Benchmarks
Australia has established progressive EUI benchmarks across various industrial sectors, reflecting our commitment to energy efficiency and sustainability. The National Australian Built Environment Rating System (NABERS) sets industry-specific targets, with current standards requiring commercial buildings to achieve an EUI of 400-600 MJ/m²/year for a 5-star rating.
Manufacturing facilities are expected to maintain EUI levels between 800-1,200 MJ/m²/year, depending on their specific operations. The food processing sector, a significant energy consumer, targets an EUI of 1,500-2,000 MJ/m²/year, with leading companies already achieving better results through innovative technologies.
The Green Building Council of Australia (GBCA) has introduced more stringent benchmarks, pushing the envelope for sustainable construction. New buildings are now expected to achieve an EUI of 300-400 MJ/m²/year to receive the highest Green Star ratings.
These standards are regularly reviewed and updated, with the Australian government’s commitment to reduce emissions by 43% by 2030 driving continuous improvement. Industry leaders like BlueScope Steel and Brickworks have demonstrated that these targets are achievable, with some facilities exceeding benchmarks through smart energy management systems and renewable energy integration.
Local councils across Australia have also adopted these standards, incorporating them into building codes and development approvals, ensuring nationwide consistency in energy performance measurement and reporting.
Bioenergy Integration and EUI Optimization
Biomass Feed Systems and Energy Efficiency
Integrating biomass feed systems into industrial operations can significantly improve energy use intensity (EUI) metrics while supporting sustainable practices. The availability of Australian bioenergy resources makes this an increasingly viable option for local businesses looking to reduce their energy footprint.
Modern biomass feed systems utilize sophisticated automation and precise material handling to optimize fuel delivery and combustion efficiency. These systems typically achieve conversion efficiencies of 80-90% when properly designed and maintained, contributing to lower overall EUI values. Key components include automated fuel handlers, moisture content monitors, and intelligent feed rate controllers that adjust to varying energy demands.
The integration of biomass systems often results in a 30-40% reduction in traditional energy consumption, particularly in industries with high thermal energy requirements such as food processing and manufacturing. Smart monitoring systems track fuel consumption patterns and adjust feed rates in real-time, ensuring optimal energy utilization.
Success stories like the Berrybank Farm Piggery in Victoria demonstrate the practical benefits of biomass integration. By implementing an advanced biomass feed system, they reduced their energy costs by 45% while improving their EUI metrics. The system converts agricultural waste into usable energy, creating a closed-loop system that benefits both the environment and the bottom line.
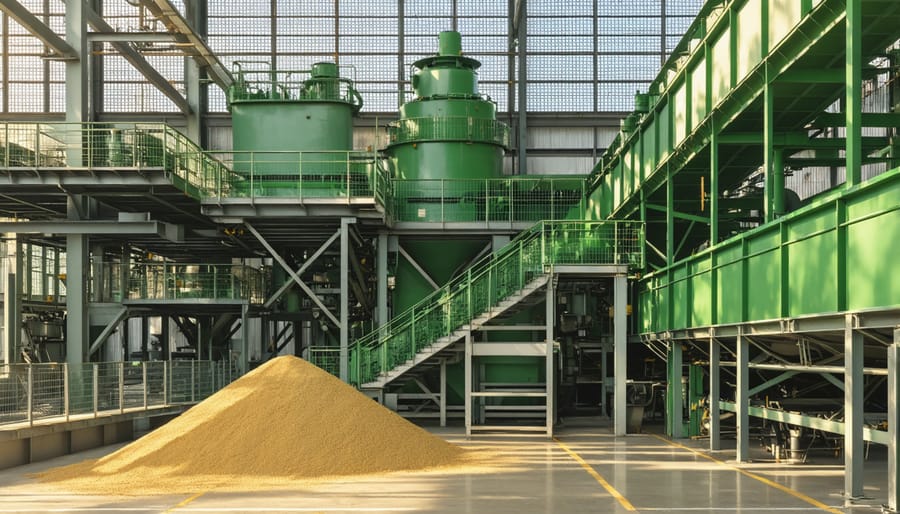
Process Heat Applications
Process heat applications represent one of the most promising areas where bioenergy can significantly improve Energy Use Intensity in industrial settings. In Australia’s manufacturing sector, companies are increasingly turning to biomass-powered systems to meet their thermal energy needs while reducing their environmental footprint.
Food processing facilities have emerged as early adopters, using agricultural waste to generate steam for cooking, sterilisation, and drying processes. For instance, a major fruit processing plant in Victoria achieved a 40% reduction in their EUI by switching from natural gas to locally-sourced fruit wood waste for their thermal operations.
The dairy industry has also embraced bioenergy solutions, particularly in cheese production and milk powder manufacturing. These facilities require consistent high-temperature process heat, which biomass boilers can efficiently provide. Several dairy processors have reported EUI improvements of 25-35% after implementing bioenergy systems.
In the timber industry, sawmills are leading the way by using their own waste products as fuel. Wood chips and sawdust that would otherwise be discarded are now powering kilns and providing space heating, creating a closed-loop energy system that dramatically improves facility EUI.
These applications demonstrate how bioenergy can deliver both environmental and economic benefits. The key to success lies in matching the right biomass resource with specific process heat requirements and implementing proper energy monitoring systems to track and optimize EUI performance.
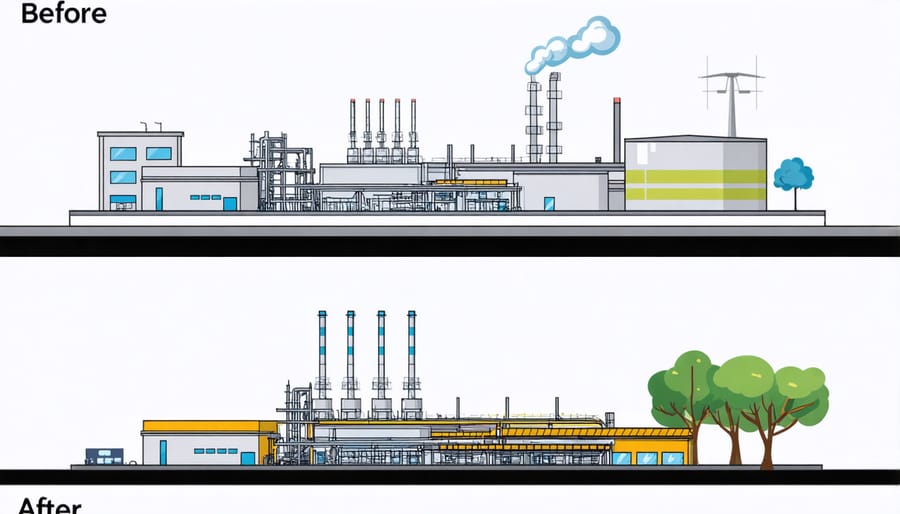
Real-World Success Stories
The transformation of Australia’s industrial landscape through bioenergy adoption has produced remarkable success stories that showcase the potential of improving Energy Use Intensity (EUI). One standout example is the Mackay Sugar Limited facility in Queensland, which reduced its EUI by 35% after implementing a bagasse-powered cogeneration system. The sugar mill now generates enough renewable energy to power its operations and exports surplus electricity to the grid, serving approximately 28,000 local homes.
In Victoria’s Goulburn Valley, SPC Ardmona’s food processing facility achieved a 40% reduction in their EUI by converting fruit waste into biogas. This innovative approach not only addressed their waste management challenges but also significantly lowered their energy costs and carbon footprint. The facility now processes over 150,000 tonnes of fruit annually while maintaining optimal energy efficiency.
The Australian Paper mill in Maryvale, Victoria, presents another compelling case study. By installing a biological treatment plant that converts wastewater into biogas, the facility decreased its EUI by 25% and reduced its reliance on natural gas. This initiative saves approximately $4.5 million in energy costs annually while preventing 39,000 tonnes of CO2 emissions.
Perhaps most impressive is the Mount Piper Brewery in New South Wales, which achieved carbon neutrality through a combination of bioenergy systems and energy efficiency measures. Their comprehensive approach included installing anaerobic digesters to process brewing waste into biogas and implementing heat recovery systems. The result was a 50% reduction in EUI and complete elimination of waste sent to landfill.
These success stories demonstrate that improving EUI through bioenergy isn’t just environmentally responsible – it’s commercially advantageous. The companies have shown that initial investments in bioenergy infrastructure typically pay for themselves within 3-5 years through reduced energy costs and increased operational efficiency. Their experiences provide valuable blueprints for other Australian industries looking to enhance their energy performance while contributing to a more sustainable future.
Implementation Strategies for Industry
Industries looking to improve their Energy Use Intensity can implement several effective strategies while integrating bioenergy solutions. The first step involves conducting a comprehensive energy audit to establish baseline measurements and identify key areas for improvement. This foundation enables organisations to develop targeted industrial carbon reduction strategies that align with their operational goals.
Smart metering and real-time monitoring systems are essential tools for tracking energy consumption patterns. These systems help facility managers identify peak usage periods and opportunities for optimization. Many Australian manufacturers have found success by implementing automated energy management systems that adjust consumption based on production demands.
Upgrading to energy-efficient equipment and incorporating waste-to-energy technologies can significantly improve EUI metrics. For instance, a food processing plant in Victoria reduced its EUI by 30% by installing a biomass boiler that converts organic waste into thermal energy.
Employee engagement programs play a crucial role in successful implementation. Training staff on energy-conscious practices and establishing clear protocols for equipment operation ensures consistent application of energy-saving measures. Creating incentive programs for departments that achieve EUI reduction targets has proven particularly effective in maintaining long-term commitment.
Regular maintenance schedules for energy-consuming equipment, combined with proper insulation of facilities and process heating systems, help prevent energy waste. Additionally, implementing heat recovery systems and exploring opportunities for cogeneration can maximize energy efficiency while reducing operational costs.
Setting realistic, incremental improvement targets and celebrating achievements helps maintain momentum in EUI reduction efforts. Many successful facilities start with small-scale pilot projects before expanding to facility-wide implementation.
Energy Use Intensity has emerged as a crucial metric in Australia’s journey toward sustainable building practices and industrial efficiency. As we’ve explored, EUI provides valuable insights into energy consumption patterns and helps organizations make informed decisions about resource management. Looking ahead, the integration of smart building technologies and artificial intelligence will further enhance our ability to monitor and optimize energy usage in real-time.
The future of EUI measurement in Australia looks promising, with increasing adoption of renewable energy solutions and improved data analytics capabilities. Organizations that embrace EUI monitoring today will be better positioned to meet upcoming environmental regulations and achieve significant cost savings. By combining EUI metrics with sustainable practices, Australian businesses can lead the way in creating a more energy-efficient future while maintaining their competitive edge in the global market.
Remember, every step toward better energy management contributes to our nation’s sustainability goals. Let’s make it count.