The global race for battery supremacy is reshaping industrial landscapes and international trade relationships at an unprecedented pace. As electric vehicles and renewable energy storage drive explosive demand for lithium-ion batteries, supply chains have emerged as the critical backbone of the energy transition. Australia, blessed with abundant lithium, nickel, and cobalt reserves, stands at a pivotal crossroads in this transformation.
From mineral extraction in Western Australia’s outback to advanced manufacturing facilities in urban centers, the battery supply chain represents a $7.4 trillion opportunity through 2050. Yet this promising future hinges on our ability to develop resilient, sustainable, and ethically sound supply networks that can withstand geopolitical pressures and market volatility.
For industry leaders and policymakers, the challenge extends beyond simply securing raw materials. It encompasses establishing processing capabilities, fostering technical innovation, building skilled workforces, and ensuring environmental stewardship throughout the value chain. As global competition intensifies and sustainability requirements tighten, Australia’s success in the battery economy will depend on strategic partnerships, technological advancement, and unwavering commitment to responsible practices.
This transformation presents not just an economic opportunity, but a chance to position Australia as a leader in sustainable battery production, supporting global decarbonization while creating thousands of skilled jobs across the nation.
Australia’s Unique Position in the Global Battery Supply Chain
Critical Mineral Advantages
Australia stands at the forefront of the global battery revolution, possessing some of the world’s most significant reserves of critical battery materials. Our nation holds approximately 30% of the world’s lithium resources and ranks among the top producers of nickel, cobalt, and rare earth elements. These natural advantages position Australia uniquely in the global battery supply chain.
The Western Australian lithium belt, stretching from the Pilbara to the Goldfields-Esperance region, represents one of the most resource-rich areas globally. Our high-grade nickel deposits in places like Kambalda and Nova-Bollinger complement these lithium resources, creating a comprehensive mineral portfolio essential for advanced battery manufacturing.
Beyond mere resource abundance, Australia’s sophisticated mining infrastructure and strong environmental regulations ensure sustainable extraction practices. This combination of rich mineral deposits and responsible mining practices makes Australia an ideal partner for international battery manufacturers seeking reliable, ethically-sourced materials. As global demand for electric vehicles and energy storage solutions continues to surge, these natural advantages become increasingly valuable for our economic future.
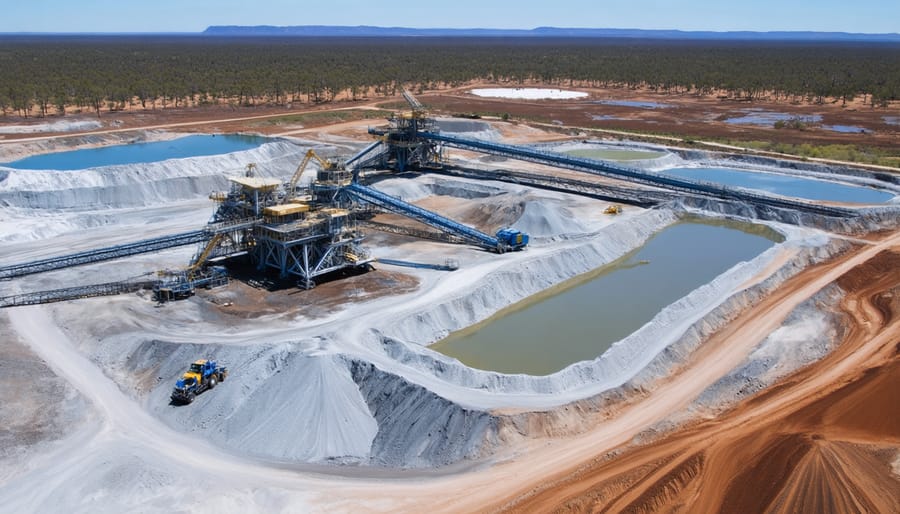
Current Manufacturing Capabilities
Australia’s domestic battery production capabilities are rapidly expanding, with several major facilities now operational across the country. The largest manufacturing hub in Queensland currently produces lithium-ion batteries with an annual capacity of 1.3 GWh, while Western Australia’s emerging battery corridor is set to double this output by 2025.
Key manufacturing centres are strategically positioned near mineral deposits and transport infrastructure, creating efficient supply networks. Modern automated production lines are capable of producing both grid-scale storage solutions and smaller residential battery units, with quality control systems meeting international standards.
Current facilities employ over 3,000 skilled workers and incorporate advanced recycling capabilities, ensuring sustainable end-of-life management. Recent investments in research and development have led to improved manufacturing processes, reducing production costs by approximately 30% over the past three years.
The industry’s growth trajectory suggests Australia is well-positioned to become a significant player in global battery manufacturing, with existing facilities operating at 85% capacity and several expansion projects underway.
Sustainable Battery Supply Chain Integration
Renewable Energy in Production
Renewable energy is revolutionising battery manufacturing in Australia, creating a more sustainable supply chain from start to finish. Leading manufacturers are increasingly powering their facilities with solar and wind energy, significantly reducing the carbon footprint of battery production. The integration of these clean energy sources not only supports environmental goals but also helps stabilise operating costs over the long term.
In Western Australia, several battery manufacturers have embraced solar power, with rooftop installations covering up to 80% of their daily energy needs. These solar arrays, combined with on-site battery storage systems, demonstrate the practical application of the very technology being produced. This circular approach to energy management is gaining traction across the industry.
Bioenergy is emerging as another promising power source for manufacturing facilities. Waste materials from agricultural and forestry operations are being converted into reliable, renewable energy. This approach not only provides sustainable power but also helps solve waste management challenges in regional areas.
Some innovative facilities are implementing hybrid systems that combine multiple renewable sources. For instance, a manufacturing plant in South Australia uses a combination of wind power, solar energy, and biogas from local organic waste to maintain continuous operations. This diversified approach ensures reliable power supply while maximising environmental benefits.
The shift towards renewable energy in battery production is creating a positive feedback loop, where cleaner manufacturing processes lead to more sustainable energy storage solutions for the future.
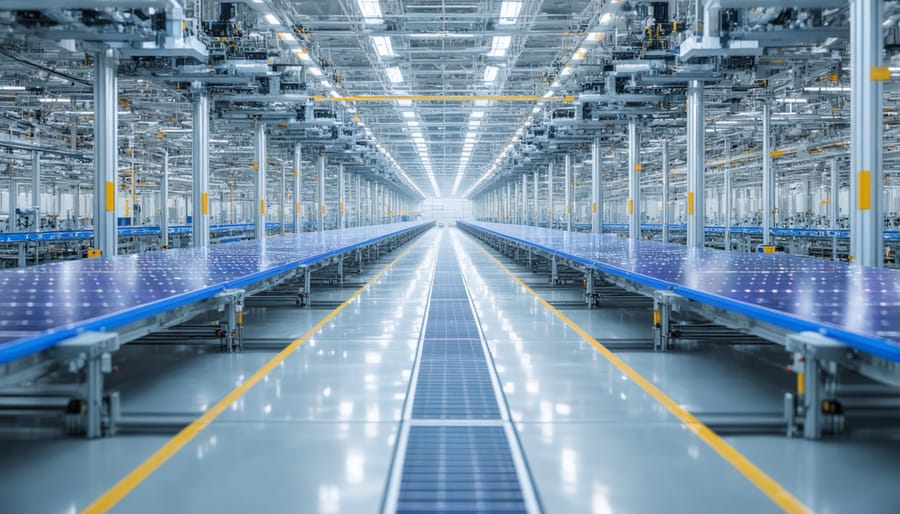
Circular Economy Practices
In Australia’s push towards a sustainable battery industry, circular economy practices are becoming increasingly vital. Leading battery recycling initiatives are transforming end-of-life batteries into valuable resources, creating a closed-loop system that benefits both the environment and the economy.
Companies across the country are implementing innovative waste reduction strategies, including designing batteries for easier dismantling and recovering critical materials like lithium, cobalt, and nickel. These recovered materials are then reintegrated into the manufacturing process, reducing the need for raw material extraction and minimizing environmental impact.
Several success stories showcase the potential of these circular practices. The Battery Stewardship Council’s B-cycle scheme has already collected over 3,000 tonnes of batteries since its launch, while advanced recycling facilities in Victoria and Western Australia are achieving recovery rates of up to 95% of battery materials.
Local manufacturers are also adopting design-for-recycling principles, ensuring their products can be easily dismantled and recycled at the end of their life cycle. This forward-thinking approach not only reduces waste but also creates new job opportunities in the recycling and remanufacturing sectors.
The implementation of these circular economy practices positions Australia as a leader in sustainable battery production, demonstrating that environmental responsibility and economic growth can go hand in hand.
Supply Chain Optimization Strategies
Digital Integration
In today’s rapidly evolving battery industry, digital manufacturing innovations are transforming traditional supply chain management into a sophisticated, data-driven ecosystem. Smart sensors and Internet of Things (IoT) devices now monitor every aspect of battery production and distribution, from raw material quality to real-time inventory tracking.
Australian battery manufacturers are increasingly adopting artificial intelligence and machine learning systems to predict maintenance needs, optimize production schedules, and reduce waste. These digital tools enable precise tracking of battery components throughout their lifecycle, ensuring quality control and maintaining transparency from mine to market.
Blockchain technology has emerged as a game-changer, providing an immutable record of battery materials’ origins and handling. This digital ledger system helps verify sustainable sourcing practices and enables better traceability of raw materials, particularly important for critical minerals like lithium and cobalt.
Cloud-based platforms are facilitating seamless collaboration between suppliers, manufacturers, and distributors. Real-time data sharing allows for quick responses to supply chain disruptions and helps maintain optimal inventory levels. Advanced analytics tools provide valuable insights for decision-making, helping companies forecast demand more accurately and adjust production accordingly.
These digital solutions not only improve efficiency but also support sustainability goals by reducing waste, optimizing energy use, and ensuring compliance with environmental standards. As Australia continues to strengthen its position in the global battery market, digital integration remains crucial for maintaining competitive advantage and environmental responsibility.
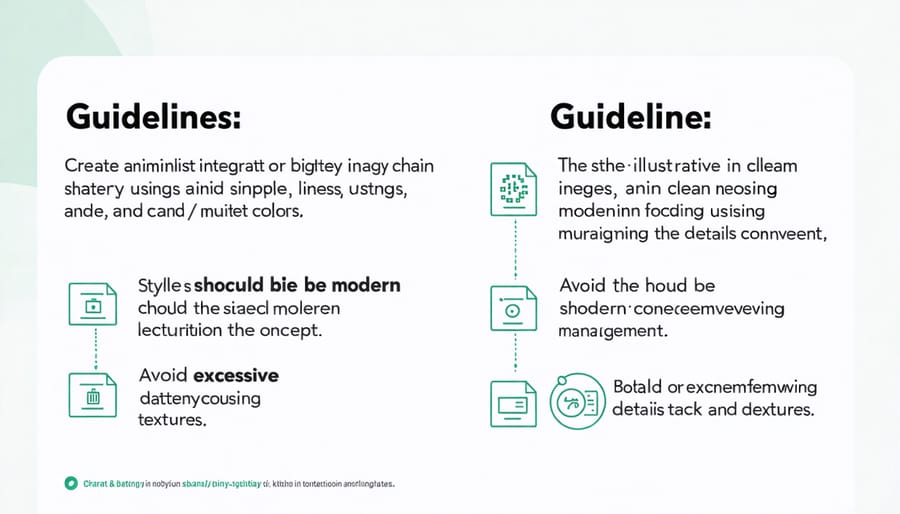
Local Manufacturing Benefits
Establishing local battery manufacturing capabilities brings numerous advantages to Australia’s economy and environment. By producing batteries domestically, we create a robust supply chain that reduces dependence on international markets while generating substantial employment opportunities across various skill levels.
Local manufacturing significantly cuts transportation costs and carbon emissions associated with importing batteries from overseas. This streamlined supply chain ensures faster delivery times and greater reliability, particularly crucial for our renewable energy projects and electric vehicle industry.
The economic ripple effects are considerable. Beyond direct manufacturing jobs, local production stimulates related industries such as mining, processing, and recycling. This industrial ecosystem fosters innovation and attracts investment in research and development, positioning Australia as a leader in battery technology.
Quality control becomes more manageable with local production, allowing manufacturers to maintain strict standards and respond quickly to market demands. This advantage is particularly valuable as battery technology rapidly evolves and consumer preferences change.
Perhaps most importantly, domestic manufacturing strengthens Australia’s energy security and sovereignty. By controlling the entire supply chain from mining to manufacturing, we’re better equipped to weather global market disruptions and ensure consistent supply for our growing renewable energy sector.
The environmental benefits extend to waste management, as local facilities can implement closed-loop recycling systems, maximizing resource recovery and minimizing environmental impact.
Quality Control Systems
Quality control in battery supply chains requires a systematic approach that begins at the raw material stage and extends through to final product delivery. Australian manufacturers have embraced world-class quality management systems, implementing rigorous testing protocols at every checkpoint to ensure batteries meet both performance and safety standards.
Leading battery producers utilize advanced testing equipment and automated inspection systems to detect defects early in the production process. These systems employ artificial intelligence and machine learning to identify subtle variations that might affect battery performance or safety. Real-time monitoring allows for immediate adjustments, reducing waste and maintaining consistent quality.
Traceability plays a crucial role in quality control, with each battery component tagged and tracked throughout the supply chain. This system enables quick identification of potential issues and streamlines the recall process if necessary. Australian manufacturers have adopted blockchain technology to enhance transparency and verify the authenticity of materials and components.
Third-party certification and regular audits ensure compliance with international standards such as ISO 9001 and specific battery safety regulations. Local testing facilities work closely with manufacturers to conduct thorough performance and safety assessments, including thermal stability tests, charge-discharge cycles, and environmental stress screening.
Environmental monitoring is integrated into quality control systems, ensuring that production processes meet sustainability targets while maintaining product quality. This dual focus on quality and sustainability has positioned Australian battery manufacturers as leaders in responsible production practices.
Future-Proofing Australian Battery Supply Chains
Emerging Technologies
Groundbreaking innovations are reshaping battery supply chains, making them smarter and more sustainable. Digital twin technology is revolutionizing manufacturing processes, creating virtual replicas of physical facilities that enable real-time monitoring and predictive maintenance. This advancement allows manufacturers to optimize production and reduce waste significantly.
Artificial Intelligence and machine learning algorithms are transforming inventory management and demand forecasting, helping companies maintain optimal stock levels while reducing storage costs. In Australia, several manufacturers are implementing blockchain technology to enhance supply chain transparency and traceability, ensuring the ethical sourcing of materials.
Advanced recycling technologies are emerging as game-changers in the battery industry. New hydrometallurgical processes can now recover up to 95% of valuable materials from used batteries, creating a more circular economy. Meanwhile, solid-state battery technology is progressing rapidly, promising to revolutionize energy storage with improved safety and performance.
Local initiatives are also exploring automated quality control systems using computer vision and AI, significantly reducing defects in battery production while increasing efficiency. These technologies are particularly crucial for Australia’s growing battery manufacturing sector, positioning the country as a leader in sustainable battery production.
Industry Collaboration
Industry collaboration is emerging as a powerful force in reshaping Australia’s battery supply chains, with partnerships spanning across mining, manufacturing, and technology sectors. Leading companies like BHP and Rio Tinto are joining forces with research institutions and innovative startups to develop more efficient extraction and processing methods.
The Battery Industry Consortium, launched in 2022, brings together key players from Western Australia’s mining sector with international technology providers to streamline production processes and reduce environmental impact. This initiative has already resulted in significant improvements in lithium processing efficiency and waste reduction.
Notable success stories include the partnership between CSIRO and local manufacturers to develop advanced recycling technologies, creating a circular economy approach to battery production. These collaborations are not just improving supply chain efficiency; they’re also generating new job opportunities and fostering technical innovation across the sector.
Small and medium enterprises are also playing their part, with regional networks forming to share resources and expertise. This collaborative approach is helping Australia maintain its competitive edge while ensuring sustainable practices remain at the forefront of industry development.
As Australia positions itself at the forefront of the global energy transition, optimizing battery supply chains stands as a crucial cornerstone for our sustainable future. The path forward demands a delicate balance of environmental stewardship, economic growth, and technological innovation. By developing robust, efficient battery supply chains, we’re not just creating jobs and boosting our economy – we’re building the foundation for a cleaner, more resilient Australia.
Our nation’s abundant natural resources, combined with our growing expertise in sustainable manufacturing and recycling, place us in a unique position to lead the battery revolution. The success stories we’re already seeing across the country, from lithium mining operations in Western Australia to advanced battery manufacturing facilities in South Australia, demonstrate our capability to create world-class supply chain solutions.
Looking ahead, the optimization of battery supply chains will play a pivotal role in Australia’s energy independence and environmental commitments. By fostering collaboration between industry players, supporting innovative technologies, and maintaining our focus on sustainability, we can ensure that our battery supply chains continue to evolve and improve.
The journey toward optimized battery supply chains is more than just an industrial challenge – it’s an opportunity to showcase Australia’s commitment to sustainability and innovation. As we continue to refine and strengthen these supply chains, we’re not just securing our energy future; we’re creating a blueprint for sustainable development that other nations can follow.