Battery safety testing stands at the forefront of Australia’s clean energy revolution, protecting both infrastructure and lives as energy storage technologies rapidly evolve. Recent incidents involving lithium-ion batteries have highlighted the critical importance of rigorous testing protocols, pushing industry standards to unprecedented levels of scrutiny.
From electric vehicles to grid-scale storage systems, every battery deployment demands comprehensive safety validation through three essential stages: cell-level testing, pack-level integration assessment, and real-world performance verification. These protocols not only safeguard against thermal runaway and electrical failures but also ensure long-term reliability in Australia’s diverse climate conditions.
Modern battery safety testing combines sophisticated thermal imaging, accelerated aging simulations, and advanced diagnostic tools to predict and prevent potential failures before they occur. This proactive approach has become increasingly vital as energy storage systems scale up to meet growing renewable energy demands across the continent.
As battery technologies continue to advance, testing methodologies must evolve in parallel, incorporating new challenges while maintaining unwavering commitment to safety standards. This dynamic relationship between innovation and security defines the future of sustainable energy storage, ensuring that progress never comes at the cost of safety.
Essential Battery Safety Tests for Modern Energy Storage
Thermal Runaway Prevention Testing
Thermal runaway prevention testing stands as one of the most crucial safety checks in battery development, particularly for Australia’s growing renewable energy sector. This rigorous testing process ensures batteries can maintain stability even under extreme conditions, preventing potentially catastrophic chain reactions that could lead to fires or explosions.
The testing procedure typically involves exposing battery cells to carefully controlled temperature increases while monitoring their behaviour. Technicians gradually heat the cells while measuring key indicators such as voltage, current, and surface temperature. Special attention is paid to the cell’s response when approaching critical temperature thresholds, usually between 80°C and 150°C depending on the battery chemistry.
To simulate real-world conditions, testing facilities employ sophisticated climate chambers that can replicate various environmental scenarios. These tests often include nail penetration tests, crush tests, and overcharge evaluations – all designed to push batteries to their limits while containing any potential failures safely.
Australian testing facilities have developed particularly stringent protocols, influenced by our unique climate challenges. These standards help ensure batteries can perform safely in our harsh conditions, from the scorching outback to humid coastal regions.
Success in thermal runaway prevention testing is measured by the battery’s ability to fail safely – meaning even if internal damage occurs, the failure remains contained and doesn’t propagate to neighbouring cells. This crucial capability has made modern batteries increasingly reliable for both residential and industrial energy storage applications.
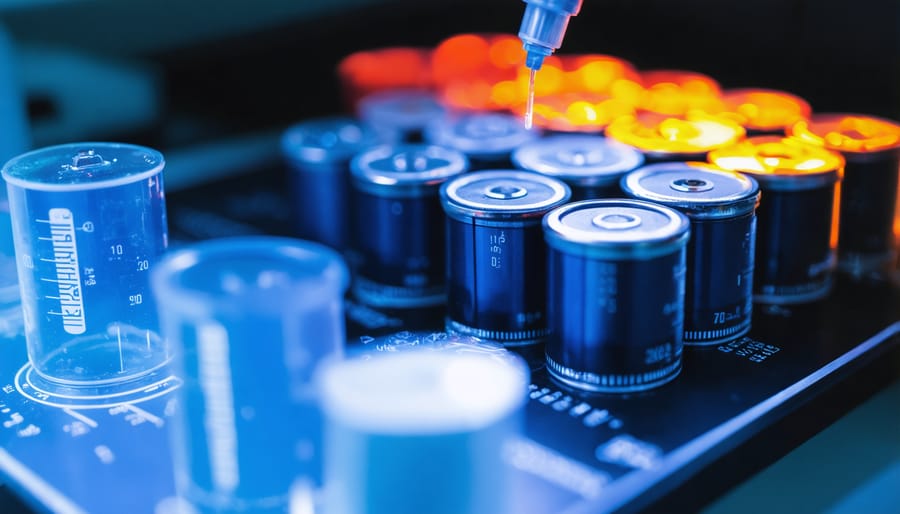
Environmental Stress Testing
In Australia’s diverse climate zones, from the scorching outback to humid coastal regions, batteries must withstand extreme environmental conditions. Environmental stress testing simulates these challenges to ensure battery safety and reliability across the continent.
Temperature testing is particularly crucial, with batteries exposed to cycles ranging from -10°C to 60°C, reflecting real-world conditions from Tasmania’s winter mornings to the Northern Territory’s summer peaks. These tests monitor battery performance, physical integrity, and chemical stability across temperature extremes, ensuring safe operation in all Australian climates.
Humidity testing addresses the unique challenges faced in tropical regions like Far North Queensland, where moisture levels can exceed 85%. Batteries undergo controlled exposure to varying humidity levels while measuring electrical performance and checking for corrosion or degradation of components.
Pressure testing simulates altitude variations experienced during transport across Australia’s diverse landscape, from below sea level at Lake Eyre to high-altitude locations in the Australian Alps. This ensures batteries maintain structural integrity and don’t leak or rupture during transportation and deployment.
Australian testing protocols also include combined stress tests, where batteries face multiple environmental challenges simultaneously. For instance, high temperature and humidity combinations common in Darwin are replicated to verify battery safety under real-world conditions.
These rigorous environmental tests help manufacturers and consumers confidently deploy battery systems across Australia’s challenging climate zones while maintaining the highest safety standards.
Australian Regulatory Framework for Battery Safety
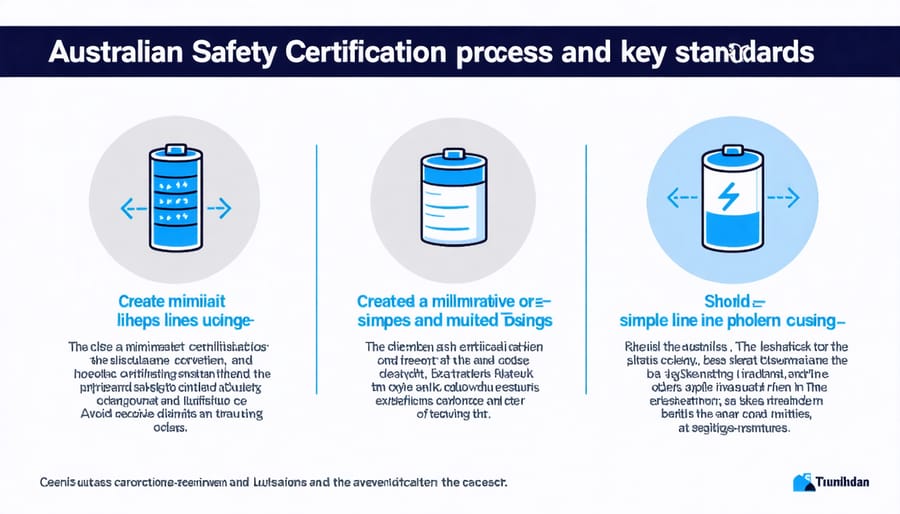
Key Safety Certifications
In Australia’s rapidly evolving energy storage landscape, compliance with Australian battery safety standards is non-negotiable for manufacturers and importers. The primary certification framework includes UN 38.3 for transport safety, IEC 62133 for secondary cells and batteries, and AS/NZS 60335.2.29 for battery chargers.
The UN 38.3 certification involves rigorous testing across eight parameters, including altitude simulation, thermal cycling, and mechanical shock resistance. This ensures batteries can withstand various environmental conditions during transport and regular use. Manufacturers must obtain this certification before shipping any lithium-based batteries internationally or domestically.
For consumer electronics and energy storage systems, IEC 62133 certification is crucial. This standard evaluates battery performance under normal and abnormal operating conditions, addressing potential hazards like overcharging, short circuits, and thermal runaway. The certification process includes comprehensive documentation of safety features and fail-safe mechanisms.
The Clean Energy Council (CEC) approval is particularly relevant for solar storage systems, requiring additional safety features specific to renewable energy applications. This certification ensures compatibility with Australian grid requirements and environmental conditions.
For electric vehicle batteries, ECE R100 certification is mandatory, focusing on vehicle-specific safety requirements including crash protection and thermal management systems. This certification includes extensive testing of battery management systems and protective enclosures.
Recent updates to these standards have incorporated enhanced fire safety requirements and cyber security considerations, reflecting the evolving nature of battery technology and its applications in sustainable energy solutions. Regular audits and compliance checks ensure ongoing adherence to these safety standards, providing peace of mind for consumers and industry stakeholders alike.
International Standards Alignment
Australia’s battery safety testing standards align closely with international benchmarks while incorporating unique requirements suited to our local conditions. The Australian Standard AS/NZS 5139:2019 harmonises with key international standards, including the International Electrotechnical Commission (IEC) guidelines and the UN Transportation Testing requirements.
A standout feature of Australian standards is their emphasis on thermal management, particularly crucial given our harsh climate. While European standards typically test batteries at temperatures up to 40°C, Australian requirements push this boundary to 50°C to account for extreme summer conditions.
Our certification process maintains reciprocal recognition agreements with major international bodies, including UL (Underwriters Laboratories) and TÜV. This means that batteries tested under these recognised international frameworks often require only supplementary testing for Australian-specific conditions rather than complete recertification.
The Australian Battery Industry Working Group actively participates in international standards development, ensuring our voice is heard in global discussions. This collaboration has led to the adoption of best practices from around the world while maintaining standards that protect consumers in our unique environment.
Recent updates to Australian standards have incorporated emerging international safety protocols, particularly regarding fire safety and thermal runaway prevention. These updates reflect global learnings from battery-related incidents and ensure Australian consumers benefit from worldwide safety innovations.
Advanced Testing Technologies
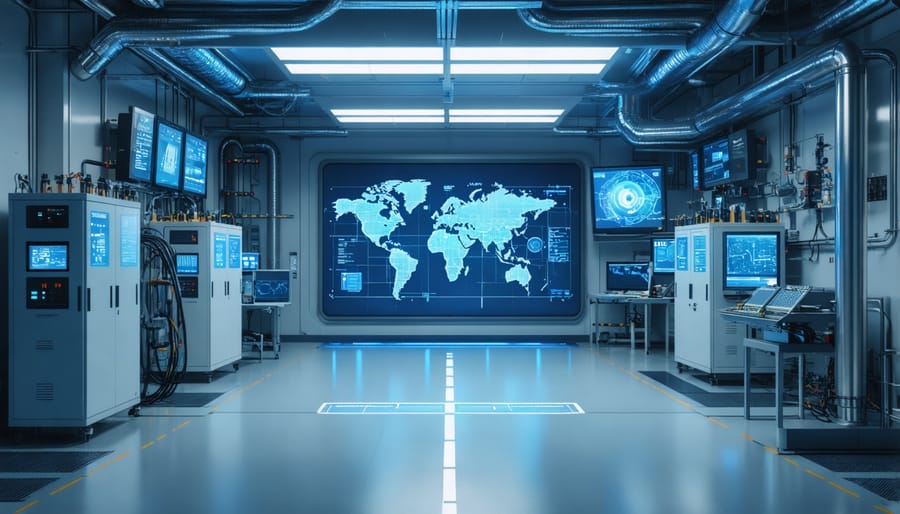
AI-Powered Safety Monitoring
Artificial intelligence is revolutionising the way we approach battery safety testing in Australia, making the process smarter, faster, and more reliable than ever before. Advanced AI algorithms now monitor battery performance in real-time, detecting subtle patterns and anomalies that might escape traditional testing methods.
These intelligent systems analyse thousands of data points per second, from temperature fluctuations to voltage variations, creating a comprehensive picture of battery health and safety. For instance, at the CSIRO’s Battery Testing Facility in Melbourne, AI-powered monitoring systems have successfully predicted potential failures days before conventional tests could detect any issues.
Machine learning models are particularly effective at identifying early warning signs of thermal runaway, a critical safety concern in lithium-ion batteries. By learning from vast datasets of battery performance histories, these systems can distinguish between normal operating variations and potentially dangerous conditions with remarkable accuracy.
The integration of AI has also streamlined the testing process for manufacturers. What once took weeks of manual testing can now be accomplished in days, without compromising on safety standards. This efficiency gain is particularly valuable for Australia’s growing renewable energy sector, where rapid deployment of safe, reliable battery storage is essential.
Local success stories include several major solar farms in Queensland, where AI monitoring systems have prevented potential battery incidents by detecting unusual behaviour patterns well before they could develop into serious problems.
Real-time Testing Systems
Modern battery safety demands continuous vigilance, and real-time testing systems are revolutionizing how we monitor and protect energy storage solutions. These advanced monitoring systems work around the clock, providing instant feedback on crucial parameters like temperature, voltage, and internal resistance. In Australia’s rapidly evolving renewable energy landscape, smart storage systems are leading the charge in implementing these sophisticated testing solutions.
These systems employ a network of sensors that continuously collect data, analyzing patterns and detecting potential issues before they become critical. Real-time monitoring allows for immediate response to any anomalies, significantly reducing the risk of thermal runaway or other safety incidents. Many Australian facilities now utilize artificial intelligence and machine learning algorithms to interpret this data, enabling predictive maintenance and enhanced safety protocols.
The beauty of real-time testing lies in its adaptability. Systems can automatically adjust testing parameters based on environmental conditions, usage patterns, and battery age. This dynamic approach ensures optimal performance while maintaining stringent safety standards. For instance, during extreme weather events – a common challenge in Australia – these systems can modify charging rates and cooling protocols to prevent stress on battery systems.
Moreover, real-time testing systems provide valuable data for improving battery design and safety protocols, contributing to the ongoing development of more reliable and efficient energy storage solutions for our renewable future.
Future of Battery Safety Testing
As we look towards the horizon of battery safety testing, exciting innovations are reshaping how we evaluate and ensure the reliability of energy storage systems. The integration of artificial intelligence and machine learning is revolutionizing testing procedures, enabling predictive analysis that can identify potential failures before they occur. These smart testing systems are particularly valuable for Australia’s growing renewable energy sector, where revolutionary battery materials are constantly being developed.
Real-time monitoring systems are becoming increasingly sophisticated, with advanced sensors that can detect minute changes in battery performance and safety parameters. This technology allows for continuous assessment rather than periodic testing, providing a more comprehensive understanding of battery behavior under various conditions.
Digital twin technology is emerging as a game-changer in the field. By creating virtual replicas of battery systems, engineers can simulate extreme conditions and stress scenarios without risking actual hardware. This approach not only saves time and resources but also enables the testing of batteries in scenarios that would be too dangerous or impractical to recreate in physical environments.
The push towards standardization is gaining momentum, with international collaboration driving the development of unified testing protocols. This global approach is particularly beneficial for Australia’s battery industry, as it helps ensure our locally manufactured products meet worldwide safety standards while maintaining competitiveness in the international market.
Automation is set to play a crucial role in the future of battery testing. Robotic systems are being developed to handle repetitive testing procedures, reducing human error and increasing testing efficiency. These systems can operate continuously, accelerating the development and certification process for new battery technologies.
Environmental considerations are also shaping future testing methods. New protocols are being developed to assess not just safety and performance, but also the environmental impact of batteries throughout their lifecycle. This holistic approach aligns with Australia’s commitment to sustainable energy solutions and responsible resource management.
As we advance, the integration of these technologies promises to make battery testing more thorough, efficient, and environmentally conscious, supporting the safe deployment of energy storage systems across our nation.
Battery safety testing stands as a cornerstone of Australia’s sustainable energy future, serving as the crucial bridge between innovation and implementation. As we’ve explored throughout this article, rigorous testing protocols not only protect consumers and businesses but also build the foundation of trust necessary for widespread adoption of battery technologies.
The journey toward a renewable energy future depends heavily on our ability to ensure the safety and reliability of energy storage solutions. From mobile devices to grid-scale installations, every battery must meet stringent safety standards before deployment. This commitment to safety testing has already enabled numerous success stories across the country, from solar-powered communities in Queensland to wind farms in South Australia.
Looking ahead, the role of battery safety testing will only grow in importance. As new technologies emerge and existing ones evolve, our testing methodologies must keep pace. The Australian battery industry has shown remarkable leadership in developing comprehensive testing protocols that are now recognized worldwide.
For manufacturers, developers, and users alike, understanding and embracing battery safety testing isn’t just about compliance – it’s about contributing to a safer, more sustainable future. By maintaining high safety standards through thorough testing, we’re not just protecting assets and investments; we’re building the confidence needed to accelerate Australia’s transition to renewable energy.
Let’s continue to champion safety testing as we work together toward a cleaner, more sustainable energy landscape for future generations.