In the race against electronic waste, the battery recycling process stands as a crucial solution for our sustainable future. Each year, millions of lithium-ion batteries reach their end of life, carrying within them valuable materials that are both environmentally hazardous and economically precious. From smartphones to electric vehicles, these power cells contain recoverable elements like lithium, cobalt, and nickel—metals that are becoming increasingly scarce and expensive to mine.
Australian recycling facilities are pioneering innovative methods to break down these complex devices, recovering up to 95% of their components for reuse. Through a combination of mechanical separation, hydrometallurgical processes, and thermal treatment, these facilities transform potential waste into valuable resources, creating a circular economy that reduces our dependence on raw material extraction.
The urgency of establishing efficient recycling systems has never been greater, as projections show Australia’s lithium-ion battery waste could reach 100,000 tonnes by 2036. By understanding and improving these recycling processes now, we’re not just managing waste—we’re securing the raw materials needed for our renewable energy future while protecting our unique environment from toxic contamination.
The Critical Need for Battery Recycling in Australia
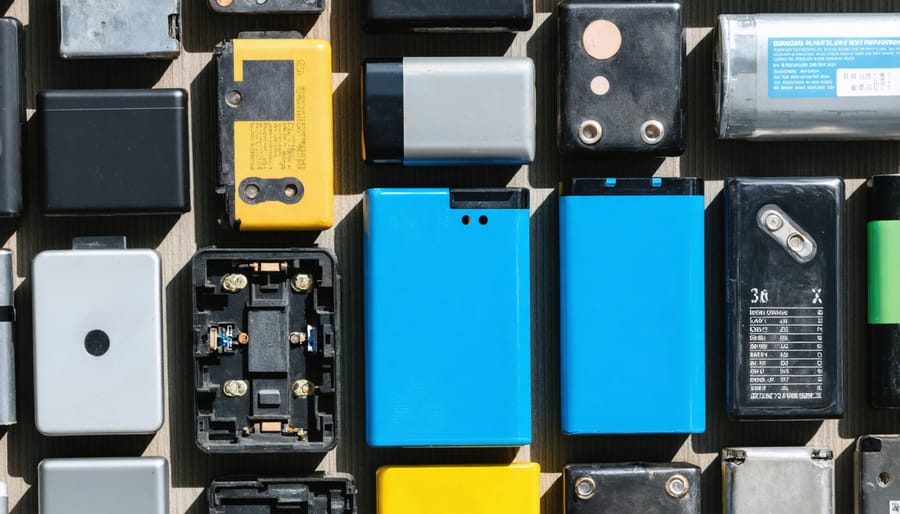
Current Battery Waste Statistics
In Australia, the challenge of battery waste is reaching critical levels, with approximately 138,000 tonnes of batteries sent to landfill annually, and this figure is projected to grow by 20% each year. Of particular concern is that only 10% of lithium-ion batteries are currently being recycled nationwide, despite their valuable and recyclable components.
The environmental impact is significant, with one incorrectly disposed lithium-ion battery capable of contaminating up to 1,000 litres of landfill groundwater. These batteries also pose fire risks in waste facilities, with several incidents reported across major Australian cities in recent years.
However, there’s room for optimism. Recent initiatives in South Australia and Victoria have shown promising results, with collection rates increasing by 50% in areas where convenient battery drop-off points have been established. Major retailers now participate in collection programs, making it easier for consumers to properly dispose of their batteries.
The Battery Stewardship Council estimates that increasing Australia’s battery recycling rate to 90% could recover materials worth $3 billion by 2036, while creating thousands of green jobs and significantly reducing our environmental footprint.
Resource Recovery Potential
Lithium-ion battery recycling offers significant potential for recovering valuable battery materials that are crucial for sustainable energy storage. The process can recover up to 95% of the battery’s core components, including lithium, cobalt, nickel, and copper, which can be reused in manufacturing new batteries or other applications.
The recovery of these materials not only reduces environmental impact but also presents substantial economic opportunities. For instance, one tonne of recycled lithium-ion batteries can yield approximately 150kg of lithium carbonate, 130kg of cobalt, and 380kg of nickel. In Australia’s context, this represents a growing opportunity, as the country’s battery consumption continues to rise with increased adoption of electric vehicles and renewable energy storage systems.
These recovered materials maintain high purity levels and can often match the quality of virgin materials, making them ideal for reuse in new battery production. This circular approach helps reduce dependency on mining raw materials while creating new jobs in the recycling industry. Many Australian recycling facilities are already demonstrating the viability of this resource recovery model, turning what was once considered waste into valuable resources for our sustainable future.
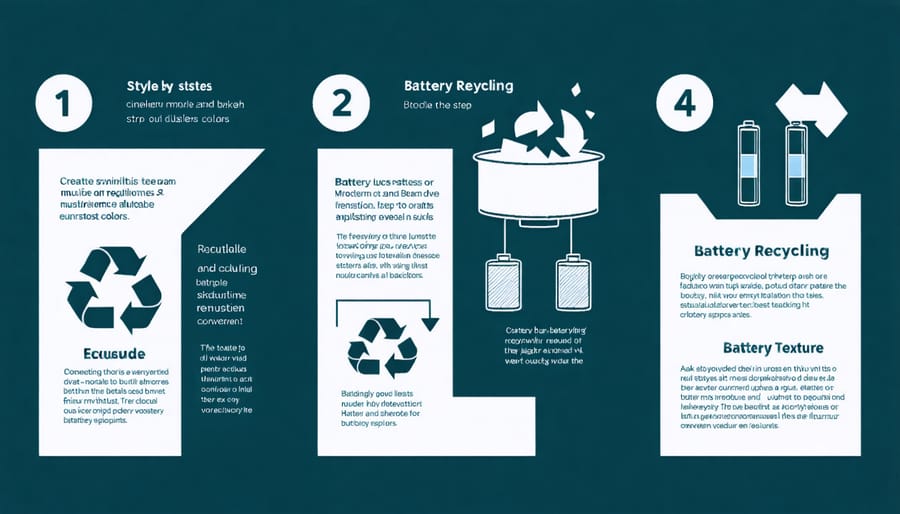
Inside the Battery Recycling Process
Collection and Sorting
The journey of recycling lithium-ion batteries begins with careful collection from various sources across Australia, including electronics retailers, council collection points, and battery drop-off locations. These collection points are strategically placed in urban and regional areas to make recycling accessible to all Australians.
Upon arrival at recycling facilities, batteries undergo a thorough sorting process. Trained technicians manually inspect and categorize batteries based on their chemistry, size, and condition. This step is crucial as different types of lithium-ion batteries require specific handling methods. Damaged or swollen batteries are isolated and handled with extra precautions to prevent safety hazards.
Advanced sorting technology, including automated systems with optical recognition capabilities, helps identify and separate batteries with different chemical compositions. This precision ensures optimal recovery rates in subsequent processing stages. The sorted batteries are then safely stored in specialized containers that prevent short circuits and contain any potential leakage.
Many Australian recycling facilities have implemented tracking systems to monitor batteries from collection to processing, ensuring transparency and accountability throughout the recycling journey. This systematic approach to collection and sorting sets the foundation for efficient resource recovery in the following stages.
Disassembly and Material Separation
The first crucial step in recycling lithium-ion batteries is their careful disassembly and separation into distinct material components. This process begins with the discharge of any remaining energy in the batteries to ensure safe handling. Skilled technicians then manually dismantle the outer casing, removing plastic shells and electronic components.
In Australian recycling facilities, automated systems are increasingly being employed to handle this task more efficiently. These sophisticated machines can process hundreds of batteries per hour, significantly reducing labour costs while maintaining high safety standards. The batteries are typically sorted by chemistry type and size before being fed into specialized crushing units.
The crushing process breaks down the batteries into smaller pieces, creating what’s known in the industry as “black mass.” This mixture contains valuable materials including lithium, cobalt, nickel, and copper. Advanced sorting technologies, including magnetic separators and density-based classification systems, then separate these crushed materials into distinct streams.
One of the most critical aspects of this stage is the separation of the cathode materials from other components. The cathode contains the highest concentration of valuable metals, making its proper isolation essential for effective recycling. Specialized vibrating screens and air classification systems help achieve this separation with remarkable precision.
Modern Australian facilities are now implementing artificial intelligence and machine learning systems to optimize this separation process. These smart systems can identify and sort different battery components with greater accuracy, ensuring maximum recovery of valuable materials while minimizing waste. This technological advancement represents a significant step forward in making battery recycling more efficient and economically viable.
Material Recovery and Purification
The material recovery and purification stage represents the heart of the battery recycling process, where valuable materials are extracted and prepared for reuse. Using hydrometallurgical processes, recyclers dissolve the black mass (crushed battery materials) in specialised acid solutions to separate different metals. This environmentally controlled process allows for the recovery of high-purity lithium, cobalt, nickel, and other valuable materials.
Australian recycling facilities employ advanced filtration and crystallisation techniques to ensure the extracted materials meet strict quality standards. For instance, the recovered lithium undergoes multiple purification steps to achieve battery-grade quality, making it suitable for manufacturing new batteries. This closed-loop approach significantly reduces the need for fresh mining while maintaining material quality.
The process also includes innovative solvent extraction methods that selectively separate different metals, achieving recovery rates of up to 95% for key materials. Many Australian facilities have implemented water recycling systems within their purification processes, minimising environmental impact and reducing operational costs.
Recent technological advances have improved the efficiency of material recovery, with some facilities now using automated sorting systems and artificial intelligence to optimise the separation process. These improvements have made battery recycling more economically viable while ensuring the recovered materials meet the high standards required by battery manufacturers.
Australian Success Stories in Battery Recycling
Leading Recycling Facilities
Australia has emerged as a leader in lithium-ion battery recycling, with several state-of-the-art facilities contributing to the nation’s clean energy revolution. Envirostream, based in Victoria, stands out as one of the country’s pioneering recycling operations, processing over 1,000 tonnes of batteries annually. Their advanced facility recovers up to 95% of battery materials, including valuable metals like lithium, cobalt, and nickel.
In New South Wales, Lithium Australia’s recycling arm, Envirostream Australia, operates a cutting-edge facility that transforms end-of-life batteries into high-value materials ready for reuse. Their innovative process not only recovers precious metals but also creates sustainable employment opportunities in the region.
Queensland’s Renewable Energy Solutions Australia (RESA) has developed a unique recycling approach that minimizes environmental impact while maximizing resource recovery. Their facility employs local workers and contributes significantly to reducing the state’s battery waste footprint.
These facilities demonstrate Australia’s commitment to sustainable battery management, with each operation implementing best-practice safety measures and environmental controls. The success of these recycling centres has attracted international attention, positioning Australia as a potential global hub for battery recycling technology and expertise.
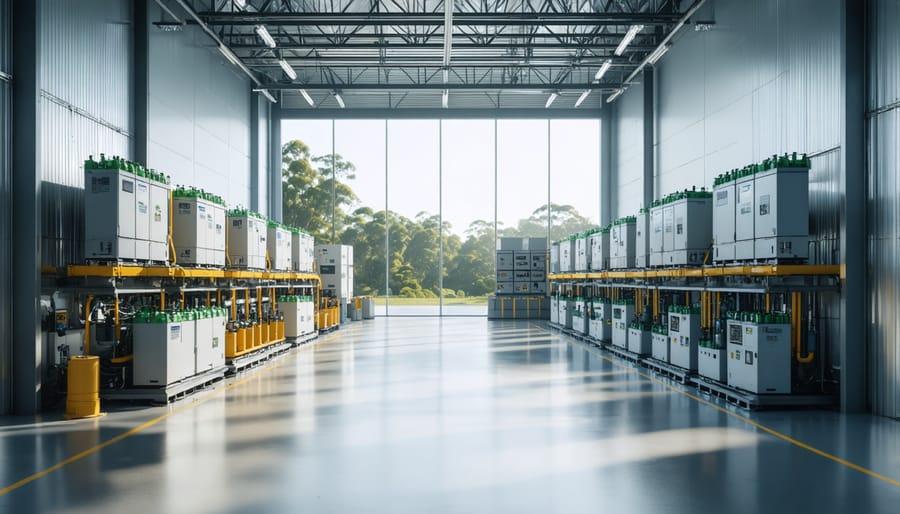
Innovation in Recycling Technology
Australian innovation in battery recycling technology has made significant strides in recent years, with several groundbreaking developments reshaping the industry. The Battery Innovation Hub in Perth has pioneered a novel hydrometallurgical process that recovers up to 95% of battery materials, setting new benchmarks for recycling efficiency.
One of the most promising developments is the “direct-to-cathode” recycling method, developed by researchers at the University of Melbourne. This process significantly reduces energy consumption by preserving the crystal structure of cathode materials, allowing them to be directly reused in new batteries without extensive reprocessing.
Local companies have also developed automated battery sorting systems using artificial intelligence and machine learning. These systems can identify and separate different battery chemistries with unprecedented accuracy, streamlining the recycling process and reducing contamination risks.
Another game-changing innovation is the mobile recycling unit concept, designed specifically for remote Australian communities. These portable facilities can process batteries on-site, eliminating the need for long-distance transportation and making recycling more accessible to regional areas.
The CSIRO has also contributed significantly by developing a bio-based extraction process that uses environmentally friendly bacteria to separate valuable metals from battery waste. This sustainable approach reduces the reliance on harsh chemicals traditionally used in battery recycling.
These innovations not only improve recycling efficiency but also create new opportunities for the circular economy while maintaining Australia’s position as a leader in sustainable technology solutions.
Future Opportunities and Challenges
The future of lithium-ion battery recycling in Australia presents both exciting opportunities and significant challenges. As electric vehicle adoption continues to surge and renewable energy storage becomes increasingly vital, the demand for efficient recycling solutions is set to skyrocket. Industry experts predict that by 2030, Australia could process up to 180,000 tonnes of lithium-ion batteries annually, creating thousands of green jobs and contributing billions to the economy.
Emerging technologies are revolutionizing how we approach battery recycling. Advanced automation and artificial intelligence are making sorting processes more efficient, while new hydrometallurgical techniques are improving material recovery rates. These innovations are particularly promising for Australia, where expanding battery safety standards and recycling infrastructure could position the country as a regional leader in sustainable battery management.
However, several challenges need addressing. The varying chemistry of different battery types makes standardized recycling processes difficult to implement. Collection and transportation logistics, especially in remote areas, remain complex and costly. Additionally, the rapid evolution of battery technology means recycling processes must constantly adapt to handle new materials and compositions.
The industry is responding creatively to these challenges. Battery manufacturers are increasingly designing for recyclability, while recyclers are developing more flexible processing methods. Partnerships between mining companies, manufacturers, and recyclers are forming to create closed-loop supply chains, ensuring valuable materials stay in circulation longer.
Looking ahead, the integration of blockchain technology for battery tracking and the development of mobile recycling units for regional areas show particular promise. These innovations, combined with growing public awareness and government support, suggest a bright future for battery recycling in Australia. The key will be maintaining the balance between technological advancement and practical implementation while ensuring environmental and safety standards continue to evolve with the industry.
As we’ve explored throughout this article, lithium-ion battery recycling isn’t just an environmental necessity – it’s a crucial step toward a sustainable future for Australia and beyond. The growing adoption of electric vehicles and renewable energy storage systems means we’re facing an unprecedented surge in battery waste. By embracing efficient recycling processes, we’re not only diverting valuable materials from landfills but also securing a domestic supply of critical resources.
The success stories we’ve seen across Australia demonstrate that battery recycling is both technically feasible and economically viable. From local council initiatives to large-scale industrial operations, these efforts are creating jobs, reducing our environmental footprint, and contributing to a circular economy.
You can be part of this positive change. Whether you’re a business owner, policy maker, or individual consumer, there are multiple ways to contribute. Start by ensuring your used batteries are properly disposed of through certified recycling programs. Support businesses that prioritize sustainable practices and battery recycling initiatives. For organizations, consider implementing battery collection points or partnering with existing recycling facilities.
The future of battery recycling in Australia is bright, but it requires collective action. By making informed choices today and supporting recycling infrastructure, we’re investing in a cleaner, more sustainable tomorrow. Let’s work together to close the loop on battery waste and create a model for responsible resource management that future generations can build upon.