As Australia’s renewable energy sector expands exponentially, industrial battery recycling emerges as a cornerstone of sustainable energy storage solutions. The global lithium-ion battery recycling market is projected to reach $38.6 billion by 2030, driving unprecedented innovation in recovery technologies and circular economy practices.
Today’s advanced recycling processes recover up to 95% of critical materials from spent industrial batteries, transforming what was once considered hazardous waste into valuable resources for manufacturing. This technological revolution isn’t just addressing environmental concerns – it’s creating a new economic frontier where sustainability meets profitability.
Australian businesses are uniquely positioned to capitalize on this opportunity, with our nation’s abundant lithium resources and growing renewable energy infrastructure. From electric vehicle batteries to grid-scale storage systems, the demand for recycled battery materials continues to soar, offering a practical solution to both resource scarcity and environmental protection.
As we transition towards a zero-waste future, industrial battery recycling represents more than just responsible waste management – it’s becoming a crucial link in the sustainable energy chain, supporting local jobs while reducing our environmental footprint.
The Growing Need for Industrial Battery Recycling
Current Battery Consumption Trends
Australia’s battery consumption has skyrocketed in recent years, driven by the rapid adoption of renewable energy systems and electric vehicles. Major industrial sectors, including mining and manufacturing, are increasingly relying on large-scale battery storage solutions, while household battery installations have doubled annually since 2020.
The mining sector leads industrial battery usage, with approximately 60% of large-scale batteries deployed in remote operations and off-grid applications. Energy storage systems for renewable projects follow closely, accounting for 25% of industrial battery consumption. The remaining 15% is distributed across manufacturing, telecommunications, and other commercial applications.
Consumer electronics and residential solar storage systems represent the fastest-growing segment of battery consumption. With over 3 million Australian households now equipped with rooftop solar, the demand for home battery storage continues to surge. This trend has created both opportunities and challenges for the recycling industry, as the volume of end-of-life batteries is projected to increase by 300% by 2030.
The shift towards lithium-ion technology across all sectors has particularly intensified the need for sophisticated recycling solutions, making it crucial for Australia to develop robust recycling infrastructure to manage this growing battery waste stream effectively.
Environmental Impact of Battery Waste
The environmental impact of improper battery disposal poses significant challenges for our ecosystems and communities. When batteries end up in landfills, they can leak harmful chemicals like lead, mercury, and cadmium into soil and waterways, contaminating our precious natural resources. These toxins can persist in the environment for decades, affecting wildlife and potentially entering our food chain.
In Australia, we dispose of roughly 14,000 tonnes of batteries annually, with many still ending up in general waste despite available battery disposal processes. The good news is that proper recycling can prevent these environmental hazards while recovering valuable materials. When batteries are recycled correctly, up to 95% of their components can be recovered and reused, significantly reducing the need for raw material extraction.
The growing adoption of electric vehicles and renewable energy storage systems makes addressing this challenge even more crucial. By implementing proper recycling practices now, we’re not just protecting our environment – we’re building a sustainable foundation for our clean energy future. Local initiatives and industry partnerships are already showing promising results in transforming potential waste into valuable resources.
Modern Industrial Battery Recycling Processes
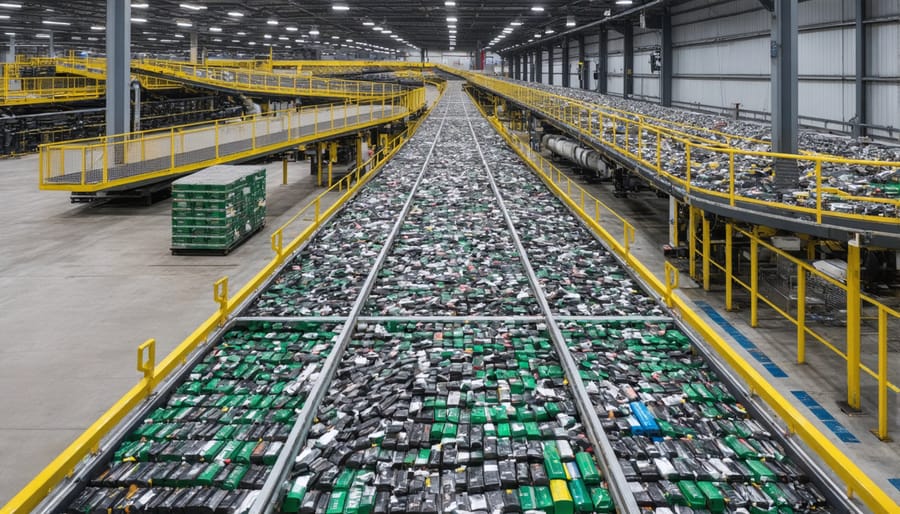
Collection and Sorting Systems
The journey of industrial battery recycling begins with efficient collection networks across Australia. Major battery manufacturers, retailers, and dedicated recycling facilities maintain collection points where businesses and organisations can deposit their end-of-life batteries. These collection points are strategically located in industrial areas, manufacturing hubs, and metropolitan centres to ensure convenient access.
Once collected, batteries undergo a thorough sorting process based on their chemical composition and size. Advanced sorting technologies, including automated systems with optical recognition capabilities, separate batteries into different categories: lithium-ion, lead-acid, nickel-cadmium, and other chemistries. This precise sorting is crucial as each battery type requires specific recycling methods to maximise material recovery and ensure safety.
Many Australian facilities now employ innovative sorting techniques, such as magnetic separation and density-based classification. These methods help identify and segregate batteries with high precision, reducing contamination risks and improving recycling efficiency. To maintain safety standards, damaged or swollen batteries are identified during sorting and handled through specialised protocols.
The sorting process also considers the state of charge of the batteries, as partially charged units can pose safety risks during recycling. Modern facilities use discharge units to safely drain any remaining energy before proceeding with the recycling process, ensuring both worker safety and optimal material recovery.
Recovery Technologies
Modern battery recycling employs several innovative technologies to recover valuable materials, each offering unique advantages for different battery types. The hydrometallurgical process, a water-based method, uses carefully controlled chemical reactions to separate and extract metals like lithium, cobalt, and nickel. This approach is particularly efficient for lithium-ion batteries and produces minimal emissions.
Pyrometallurgical recovery, involving high-temperature smelting, excels at processing mixed battery types and recovering precious metals. While energy-intensive, this method effectively handles large volumes and recovers materials with high purity levels. Leading Australian recycling facilities often combine both methods to maximise recovery rates and minimise environmental impact.
Mechanical separation has emerged as a game-changer in recent years. This process begins with crushing and sorting batteries into their component materials using advanced sensors and automated systems. The resulting materials undergo further refinement through magnetic separation, density sorting, and screening.
Direct recycling, the newest innovation in the field, aims to recover cathode materials in their original form, significantly reducing processing costs and energy consumption. Several Australian facilities are pioneering this technology, achieving recovery rates of up to 95% for some battery components.
These technologies continue to evolve, with researchers developing more efficient and environmentally friendly methods. The focus remains on maximising material recovery while minimising energy use and environmental impact, supporting Australia’s circular economy goals.
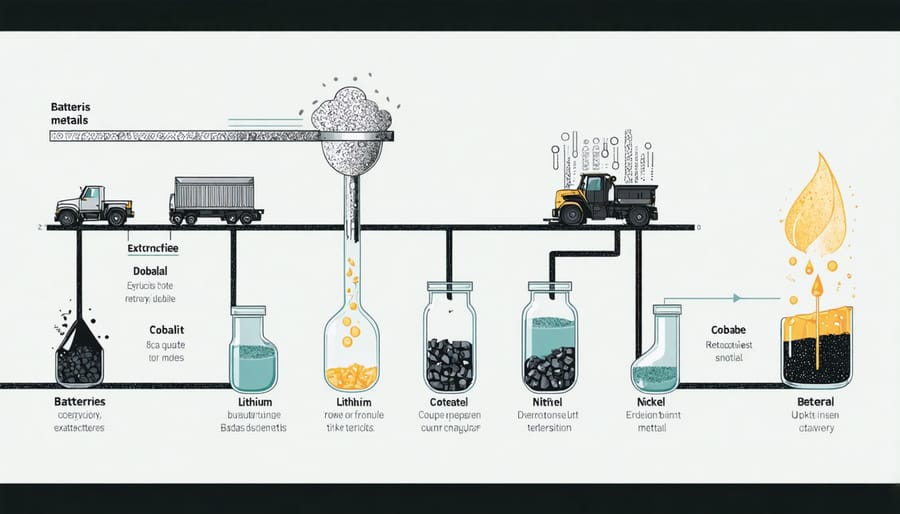
Material Reintegration
The journey from recovered battery materials to new manufacturing inputs is a remarkable example of circular economy in action. Once materials are extracted and sorted, they undergo rigorous refinement processes to meet industry specifications for reuse. Battery-grade lithium, cobalt, and nickel must achieve 99.9% purity levels before they can be integrated into new battery production.
In state-of-the-art facilities across Australia, sophisticated chemical processes transform these recovered materials into high-value products. Lithium compounds are processed into lithium carbonate or lithium hydroxide, essential for new battery cathodes. Cobalt and nickel undergo hydrometallurgical treatment to create pure metal sulfates, while copper and aluminium are refined to meet electrical conductor standards.
What’s particularly exciting is how these reintegrated materials perform just as well as virgin materials in new batteries. Leading manufacturers report no difference in performance between batteries made with recycled materials and those made with newly mined resources. This breakthrough has created a reliable secondary supply chain that reduces our dependence on mining while maintaining product quality.
The reintegration process also includes quality control measures at every step, ensuring that recycled materials meet or exceed industry standards. With advanced tracking systems, manufacturers can now certify the percentage of recycled content in their batteries, meeting growing consumer demand for sustainable products.
Benefits for Australian Industry
Resource Security
Battery recycling plays a crucial role in reducing Australia’s dependence on imported raw materials, particularly critical minerals like lithium, cobalt, and nickel. As the Australian battery manufacturing industry continues to grow, establishing robust recycling infrastructure becomes increasingly vital for our resource security.
By recovering valuable materials from end-of-life batteries, we can create a circular economy that decreases our reliance on international supply chains. This self-sufficiency is particularly important given global market volatility and increasing competition for battery materials. For instance, recycling just one tonne of lithium-ion batteries can recover up to 35kg of lithium, 333kg of steel, and significant amounts of other precious metals.
Local recycling facilities are already demonstrating impressive recovery rates, with some achieving up to 95% material reclamation. This not only secures a domestic supply of critical materials but also creates new jobs and economic opportunities within Australia. The development of these recycling capabilities provides a buffer against international supply disruptions and price fluctuations, ensuring the continued growth of our renewable energy sector.
For Australian businesses and communities, this means greater energy security and reduced exposure to global market pressures. It’s a smart investment in our future that helps safeguard our resources while supporting our transition to renewable energy.
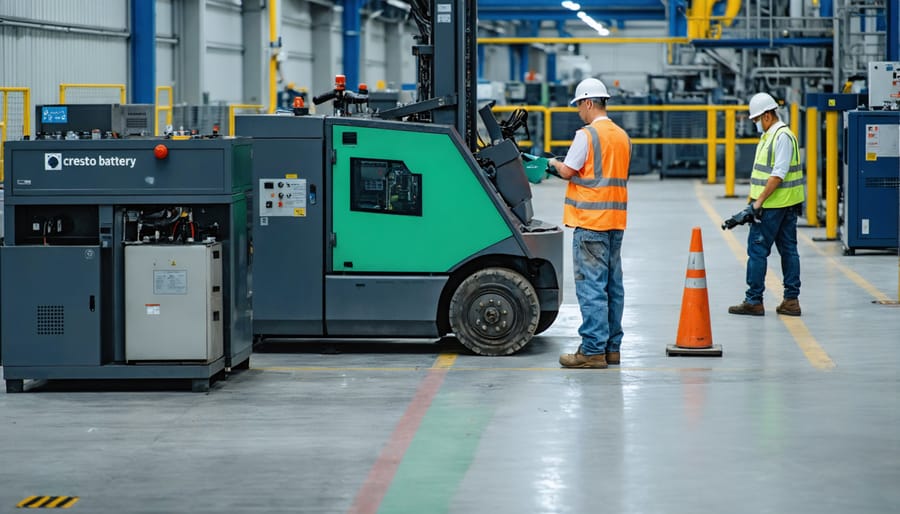
Job Creation and Economic Growth
The industrial battery recycling sector is emerging as a significant contributor to Australia’s job market and economic landscape. As the renewable energy sector continues to grow, battery recycling facilities are creating diverse employment opportunities across multiple skill levels. From collection and sorting specialists to chemical engineers and environmental compliance officers, the industry is generating sustainable careers that combine technical expertise with environmental stewardship.
In regional areas, battery recycling facilities are becoming economic catalysts, providing both direct and indirect employment opportunities. For every job created within a recycling facility, an estimated 2.8 additional jobs are generated in supporting industries such as transportation, maintenance, and technical services. This multiplier effect strengthens local economies and promotes regional development.
The economic benefits extend beyond employment. The recovery of valuable materials like lithium, cobalt, and nickel creates new revenue streams and reduces dependency on raw material imports. Australian recycling facilities are projected to generate over $3 billion in economic activity by 2030, with exponential growth expected as electric vehicle adoption increases.
Innovation in the sector is attracting investment and fostering entrepreneurship. Start-ups focusing on advanced recycling technologies are securing funding, while established companies are expanding their operations. This growth is complemented by increasing demand for training programs and specialized certifications, creating pathways for workforce development and skills enhancement in the green economy.
Future Innovations and Opportunities
Emerging Technologies
The landscape of battery recycling is rapidly evolving, with groundbreaking technologies reshaping how we approach the end-of-life management of energy storage systems. Australian researchers are at the forefront of developing innovative battery materials and recycling processes that promise to revolutionise the industry.
Direct recycling technology has emerged as a game-changer, allowing the recovery of cathode materials without breaking down their crystal structure. This method significantly reduces energy consumption and maintains the high value of recovered materials. Another promising development is ultrasonic separation, which uses sound waves to efficiently sort battery components while minimising chemical waste.
Automated dismantling systems, powered by artificial intelligence and robotics, are making the recycling process safer and more efficient. These systems can process various battery types at high speeds while protecting workers from hazardous materials. Additionally, bio-leaching techniques using naturally occurring bacteria are showing tremendous potential for extracting valuable metals in an environmentally friendly way.
These emerging technologies are expected to slash recycling costs by up to 60% while increasing recovery rates to over 90% for most battery materials, making sustainable battery management more accessible than ever before.
Industry Growth Prospects
The industrial battery recycling sector is poised for remarkable growth, driven by the booming electric vehicle market and increasing adoption of renewable energy storage systems. Industry analysts project the global battery recycling market to expand at a compound annual growth rate of over 18% through 2030, with Asia-Pacific leading the charge.
In Australia, the future looks particularly promising. The federal government’s commitment to net-zero emissions by 2050 has catalysed investment in battery recycling infrastructure. Major players are establishing state-of-the-art facilities across the country, with several companies already announcing plans for new recycling plants in Victoria and Western Australia.
The rise of urban mining – extracting valuable materials from discarded batteries – presents a golden opportunity for the sector. With lithium-ion batteries containing precious metals like cobalt, nickel, and lithium, recycling is becoming increasingly economically viable. Industry experts predict that by 2025, recycled materials could meet up to 25% of the battery industry’s raw material demands.
Technological advancements in recycling processes, coupled with strengthening regulatory frameworks, are creating a perfect storm for industry growth. This evolution isn’t just good business – it’s essential for creating a sustainable circular economy in the energy sector.
Industrial battery recycling stands as a cornerstone of Australia’s journey toward a sustainable future. As our nation continues to embrace renewable energy solutions and electric vehicles, the importance of responsible battery management becomes increasingly critical. Through innovative recycling processes, we’re not just reducing landfill waste – we’re securing a sustainable supply chain for valuable materials like lithium, cobalt, and nickel.
The success stories emerging from Australian recycling facilities demonstrate that with the right infrastructure and commitment, we can create a circular economy that benefits both the environment and our economy. By recovering and reusing battery materials, we’re reducing our dependence on raw material extraction while creating new jobs and opportunities in the green technology sector.
Looking ahead, the growth of industrial battery recycling will play a vital role in meeting our national sustainability targets and supporting the renewable energy transition. It’s a prime example of how innovative thinking and environmental responsibility can work hand in hand with economic progress.
For businesses, governments, and communities across Australia, supporting and investing in battery recycling infrastructure isn’t just an environmental imperative – it’s a smart strategic move that positions our nation as a leader in sustainable resource management. Together, we can build a future where every battery reaches its full potential through efficient recycling and recovery, creating a legacy of environmental stewardship for generations to come.